纳米ZrB2 增强CoNiCrAlY复合粉末的机械合金化制备及其涂层的组织与性能
Mechanical Alloying Fabrication of Nano-ZrB2-Reinforced CoNiCrAlY Composite Powders and Microstructure-Property Characterization of the Resultant Coatings
通讯作者: 张世宏,shzhang@ahut.edu.cn,主要从事金属表面科学与技术研究
责任编辑: 李海兰
收稿日期: 2023-04-21 修回日期: 2023-05-24
基金资助: |
|
Corresponding authors: ZHANG Shihong, professor, Tel:
Received: 2023-04-21 Revised: 2023-05-24
Fund supported: |
|
作者简介 About authors
杨 康,男,1994年生,博士
针对高温炉辊在高温重载环境下的氧化、磨损等失效问题,采用一步式和分步式机械合金化(MA)工艺分别合成了2种CoNiCrAlY-20%ZrB2 (质量分数)复合粉末并制备成涂层,对其组织和性能进行了研究。结果表明,用分步式MA成功合成了纳米ZrB2增强的CoNiCrAlY复合粉末,较一步式球磨,分步式球磨的ZrB2颗粒更加均匀地分布在金属基体相中。分步式MA球磨35 h复合粉末的平均粒径符合超音速火焰喷涂(HVOF)要求。采用HVOF制备复合涂层,发现分步式MA粉末制备的涂层熔化状态较一步式MA粉末制备的涂层更好,且分步式涂层孔隙率更低、硬度更高、韧性更强。2种涂层在750 ℃以上均具有良好的自润滑能力,且在950 ℃时涂层表面形成了连续完整的“上釉层”。950 ℃时分步式涂层磨损率比一步式涂层低了60%,说明在高温环境下分步式涂层具有更好的耐磨性能。此外,与纯CoNiCrAlY涂层相比,纳米ZrB2颗粒加入可以显著提升涂层的高温摩擦磨损性能。
关键词:
High-temperature furnace rolls are subjected to extreme conditions, including high temperatures and heavy loads, rendering them susceptible to oxidation, wear, and other forms of failure. To address these issues, this study investigates the preparation and properties of CoNiCrAlY-ZrB2 composite powders and coatings. CoNiCrAlY serves as the metal matrix, and ZrB2 acts as the ceramic reinforcement phase. Two variants of CoNiCrAlY-20%ZrB2 (mass fraction) composite powders were fabricated using one-step and step-fashion mechanical alloying (MA) techniques (marked by MA-1 and MA-2, respectively). The microstructure and phase composition of the coatings were studied using SEM, XRD, and TEM. Mechanical properties were also investigated. High-temperature friction and wear tests were conducted at 550-950 oC. Results indicate that the particle size of the composite powder decreases with increasing MA time. Step-fashion MA successfully produced ZrB2-reinforced CoNiCrAlY composite powder, with ZrB2 particles evenly distributed throughout the CoNiCrAlY matrix. When alloyed for 35 h, the average particle size (D50 = 38.6 μm) met the specifications for high-velocity oxygen-fuel (HVOF) spraying. CoNiCrAlY-20%ZrB2 composite coatings were then prepared via HVOF spraying. Coatings derived from MA-2 powders exhibited higher melting states, denser microstructures, and lower porosity (0.28%) compared to those made with MA-1 powders. These coatings also displayed superior hardness (738 HV0.3) and fracture toughness (5.21 MPa·m1/2). High-temperature wear resistance was tested for both MA-1 and MA-2 composite coatings. At 950 oC, a protective glazing layer of Al2O3, Cr2O3, and CoCr2O4 was formed on the surface of the composite coatings. The coatings demonstrated effective self-lubrication at 750 oC due to the formation of the “glazing layer”. Above 750 oC, the MA-2 composite coating outperformed the one-step coating in wear resistance. Specifically, at 950 oC, the wear rate of the MA-2 composite coating was 1.71 × 10-14 m3·N-1·m-1, considerably lower than that of the MA-1 composite coating (4.28 × 10-14 m3·N-1·m-1). In conclusion, the addition of ZrB2 nanoparticles to the CoNiCrAlY coating considerably enhanced its friction and wear properties at high temperatures. The step-fashion mechanical alloying method demonstrated superior coating density, hardness, and high-temperature wear resistance.
Keywords:
本文引用格式
杨康, 辛越, 姜自滔, 刘侠, 薛召露, 张世宏.
YANG Kang, XIN Yue, JIANG Zitao, LIU Xia, XUE Zhaolu, ZHANG Shihong.
21世纪以来,随着汽车、轮船、飞机行业的飞速发展,对高质量带钢的需求日益增加,并对带钢的表面质量提出了更为严苛的要求。带钢的表面质量与连续退火炉生产线(CAL)及连续热镀锌生产线(CGL)中的核心部件——高温炉辊密切相关。在带钢的生产过程中,首先需要通过辐射加热的方式对带钢进行加热(900~1100 ℃),且带钢在输送过程中有着较高的载荷摩擦作用,在这种工作环境下炉辊表面发生的氧化、磨损、结瘤会直接影响带钢的表面质量。造成炉辊损坏的原因主要有以下几个方面[1]:(1) 在带钢对炉辊辊面的冲击和较高的载荷摩擦作用下,造成辊面摩擦损耗形成刮痕,从而会影响钢板表面质量;(2) 炉内的温度较高,尽管炉内有还原性气氛的保护,长期处于高温状态下的炉辊仍不可避免会发生氧化;(3) 带钢表面的氧化物在炉内被还原成Fe,升高到一定温度后与炉辊表面的材料发生反应,黏附在炉辊表面形成积瘤。随着长时间的高速运转,积瘤增大同时磨损加剧,在与钢板接触时易产生划痕及压坑,损伤钢板表面。为满足高温炉辊苛刻的工况要求,高温炉辊防护涂层必须具有耐磨、耐冲击和良好的抗氧化及燃气侵蚀等特性。MCrAlY (M = Co、Ni或Co + Ni)涂层因其在高温下具有优异的抗高温氧化和耐热腐蚀性能、良好的塑性、与基材的结合较好等特点,被广泛应用于航空航天和机械制造等领域[2]。然而,单一MCrAlY涂层的耐磨性能较差,严重限制了其进一步应用。为了克服这一问题,在MCrAlY涂层中加入Al2O3、ZrO2、TiB2等陶瓷增强相制得金属陶瓷涂层[3~5],以充分发挥金属相的强韧性和陶瓷相的耐磨耐蚀性。
本工作分析了一步式和分步式MA方法对CoNiCrAlY-ZrB2复合粉末形貌、粒度及陶瓷分布的影响。采用2种MA工艺获得满足HVOF粒度要求的复合粉末,使用HVOF制备高质量的复合涂层,并研究其微观组织、力学性能(包括显微硬度、断裂韧性及结合强度等)。通过对比研究纯CoNiCrAlY涂层、一步式MA涂层和分步式MA涂层,评价复合涂层的高温摩擦磨损性能,并通过涂层组织演变与物相分析,揭示复合涂层的高温耐磨损机理。
1 实验方法
1.1 实验材料
实验使用的CoNiCrAlY粉末粒径为15~45 μm,硼化物陶瓷粉末选用ZrB2粉末,其粒径分布范围为1~3 μm,粉末的具体化学成分见表1。
表1 CoNiCrAlY粉末及ZrB2陶瓷粉末化学成分 (mass fraction / %)
Table 1
Powder | Co | Ni | Cr | Al | Y | B | Zr |
---|---|---|---|---|---|---|---|
CoNiCrAlY | Bal. | 30-34 | 20-23 | 6-10 | 0.4-0.7 | - | - |
ZrB2 | - | - | - | - | - | 0.5 | 99.5 |
1.2 复合粉末及涂层的制备
采用QXQM-6型行星式球磨机制备复合粉末,并采用一步式及分步式MA方法(2种工艺分别记为MA-1和MA-2)制备20%ZrB2-CoNiCrAlY (质量分数,下同)复合粉末。在一步式机械合金化方法中,直接将20%ZrB2陶瓷粉末与80%CoNiCrAlY金属粉末混合作为初始粉末,置于球磨罐中,在相同的条件下分别研磨25、30、35和40 h。在分布式MA方法中,以ZrB2含量为10%的CoNiCrAlY-ZrB2混合粉末为起始球磨材料,分别在球磨至15和20 h时,相继加入5%ZrB2陶瓷颗粒,最终使ZrB2颗粒的质量比达到20%,然后继续球磨至25、30、35和40 h。球磨前对罐体进行抽真空后通入Ar气保护气氛,磨球选用直径分别为15、10、6和5 mm的高Cr钢球,对应磨球质量比为1∶4∶2∶1,球料配比为10∶1,球磨转速为220 r/min。采用过筛分级设备筛选出15~45 μm粒径范围的复合粉末以满足HVOF的粒度要求。
采用ZB-2000 HVOF设备分别制备纯CoNiCrAlY涂层及CoNiCrAlY-ZrB2复合涂层。使用O2-煤油作为燃料系统,Ar气作为载气,装配喷枪为JP5000型,循环水为冷却剂进行操作。喷涂距离为380 mm,喷枪的扫描速率800 mm/s,O2流量900 L/min,煤油流量26 L/h,送粉率50 g/min。此外,喷涂前需要对基体进行净化处理(丙酮超声清洗)、喷砂处理,喷砂为60目棕刚玉(粒度0.25 mm),压缩空气压力在0.6~0.8 MPa之间,喷砂距离100~120 mm,喷砂角度60°~80°。
1.3 微观组织表征
使用Phenom XL型扫描电子显微镜(SEM)以及自带的能谱仪(EDS)表征粉末形态、截面微观组织及涂层的表面和截面形貌;使用Tecnai G2 F20透射电子显微镜(TEM)观察喷涂态涂层的组织结构,并用电镜自带的EDS进行元素分析;使用MASTERSIZER 2000型激光粒度分析仪表征不同球磨时间CoNiCrAlY-ZrB2复合粉末的粒度分布;使用UItima IV型X射线衍射仪(XRD)对粉末和涂层进行物相分析,扫描范围20°~80°,扫描速率10°/min;使用LabRAM HR Evolution HORIBA Jobin-Yvon氩离子激光源的Raman光谱仪在532 nm激发波长下测定高温磨损后磨痕的物相;利用Image J软件处理涂层截面SEM图像得到对应涂层的孔隙率。
1.4 性能测试
按照GB/T 9790—2021标准,使用具有Vickers金刚石压头的MH-5LD型显微硬度测试仪测量涂层磨抛后截面的显微硬度(H),载荷为3 N,保压时间15 s。涂层的断裂韧性(KIC)采用压痕法测量,KIC的计算公式为:
式中,P为载荷压力,N;a为菱形压痕中心到对角线末端的距离,μm;c为菱形压痕中心到裂纹尖端的距离,μm。
按照GB/T 8642—2002标准,采用胶结拉伸法测量复合涂层的结合强度。复合涂层的摩擦磨损性能测试使用UMT-Tribolbab型球盘式摩擦试验机,采用直径6.35 mm的Si3N4球作为摩擦副材料,滑动实验的载荷为10 N,转速364 r/min,旋转半径3.5 mm,温度分别为550、750和950 ℃,实验时间60 min。通过SEM观察复合涂层的磨痕形貌,并使用EDS进行元素分析。通过Alphastep P-7探针接触式轮廓仪测算涂层的磨损总体积(Vm),并使用下式计算涂层的磨损率(K):
式中,F为加载力,N;d为旋转半径,m;R为转速,r/min;T为运行时间,min。
2 实验结果
2.1 不同球磨时间下一步式与分步式机械合金化对粉末质量的影响
图1分别给出了不同球磨时间下MA-1和MA-2工艺制备的复合粉末原始微观形貌SEM像。由图1可知,2种MA工艺制备的粉末形貌具有相似的演变规律,即随着球磨时间的延长,CoNiCrAlY-ZrB2复合颗粒的尺寸不断减小。但是在相同球磨时间下,粉末的粒径尺寸和形貌并不相同。对于MA-1工艺,当球磨时间为25 h时,由于颗粒发生反复的塑性变形、破碎和冷焊,粉末大多呈现出不规则的扁平状形貌且粒径分布不均匀,如图1a所示。当球磨时间达到30 h时,大尺寸的颗粒被进一步破碎,粉末粒径趋于一致且表现为流动性更好的椭球形形貌,如图1b所示。随着球磨时间的继续延长,球磨破碎作用占据主导地位,粉末被进一步破碎细化,如图1c和d所示。
图1
图1
球磨不同时间后一步式和分步式机械合金化(MA-1和MA-2)工艺制备的复合粉末筛分前表面形貌SEM像
Fig.1
Surface SEM images of composite powders fabricated by one-step mechanical alloying (MA-1) (a-d) and step-fashion mechanical alloying (MA-2) (e-h) before sieving after different ball milling time
(a, e) 25 h (b, f) 30 h (c, g) 35 h (d, h) 40 h
采用MA-2工艺制备的CoNiCrAlY-ZrB2复合粉末在球磨25 h后颗粒出现了明显的长大,部分颗粒尺寸达到约80 μm,远大于原始合金颗粒的尺寸(15~45 μm),如图1e所示。这说明粉末在机械合金化初期以塑性变形和冷焊为主导,与MA-1工艺存在明显差异。这是由于在机械合金化过程中,不仅存在磨球-粉末、罐壁-粉末的作用,同时还存在粉末-粉末间的作用,特别是在球磨的初始阶段引入大量游离的硬质陶瓷颗粒,其对金属颗粒的助磨效果明显,并导致粉末细化。而采用MA-2工艺时,由于在前期只引入少量的陶瓷相,金属相颗粒优先发生塑性变形和破碎,使颗粒表面变得粗糙,更有利于黏附细小的陶瓷颗粒,因此后续加入的陶瓷粉末会率先被金属相包覆而不是游离在罐体内部,从而延缓金属相颗粒发生破碎的程度,使得冷焊成为前期的主导作用。然而随着球磨时间的延长(30和35 h),焊合长大的颗粒不可避免地发生破碎,同时粉末的形态由扁平状逐步转化为椭球状,如图1f和g。当球磨时间达到40 h时,粉末的整体尺寸过小不再符合热喷涂的要求[13],如图1h所示。
由于CoNiCrAlY和ZrB2复合颗粒属于韧性-脆性体系,韧性CoNiCrAlY粉末在磨球的挤压和碰撞下发生剧烈的塑性变形,导致其球形逐渐消失,随后与脆性相ZrB2颗粒形成近球形的复合粉体。这一过程主要取决于以下2个因素:首先,由于磨球传递的动能有限,较小的颗粒难以粉碎,磨球的摩擦作用使粉末再次变成球形结构;其次,由于冷焊和静电力而聚集成球形的小颗粒会导致表面能降低。总而言之,尽管同时存在破碎和团聚,但粉末粒度会随着连续球磨而降低,当其减小到一定程度时,它们之间就会出现动态平衡。因此,粉末粒度不会再发生明显变化并保持相对稳定[14]。
通常情况下,球磨时间越长,机械合金化的均匀程度越好,但是过长的球磨时间会导致粉末粒径的过度减小。本工作中,符合热喷涂粉末要求的粒径尺寸以及高的成粉率被作为判断最佳球磨时间的依据。图2a给出了2种MA工艺制备的CoNiCrAlY-ZrB2粉末筛分后的平均粒径(D50)。可见,MA-1粉末的D50随时间延长逐渐减小,且球磨30 h的复合粉末平均粒径(D50 = 39.5 μm)与商用CoNiCrAlY粉末(38.9 μm)最为相近。图2b为复合粉末筛分后粒径在15~45 μm范围内的质量占比。可以看出,球磨30 h的复合粉末成形率最高,此时制备粉末的MA工艺效率最好。MA-2粉末的D50随球磨时间延长而逐渐减小。球磨35 h后复合粉末的平均粒径(D50 = 38.6 μm)与商用CoNiCrAlY粉末最为接近,粒径范围在15~45 μm之间的粉末约占74%,如图2b所示。经过40 h球磨后,复合粉末的D50急剧下降,不再符合热喷涂的粒径要求。与MA-1工艺结果对比发现,相同的球磨时间下采用MA-2工艺制备的复合粉末粒度和成粉率均优于MA-1工艺制备的粉末,说明分步添加硬质陶瓷颗粒的方法能够有效抑制粉末粒度减小,使得更高比例的粉末符合热喷涂粒径要求。
图2
图2
球磨不同时间后MA-1、MA-2复合粉末的平均粒径(D50)及筛分后质量占比
Fig.2
Average diameters (D50) (a) and percentages after sieving (b) of MA-1 and MA-2 composite powders after different ball milling time
图3分别为一步式球磨30 h和分步式球磨35 h MA制备的复合粉末截面形貌及EDS元素分布,图中的浅灰色相和白色颗粒分别是CoNiCrAlY和ZrB2。由图3a和b可知,一步式球磨30 h的粉末截面呈明显的层状结构,粉末内部存在大量无ZrB2颗粒嵌入的层状CoNiCrAlY金属相区域,ZrB2颗粒分布不均匀。由图3c和d可知,分步式球磨35 h的粉末内部有大量的白色ZrB2颗粒,它们均匀地分散在浅灰色的CoNiCrAlY金属相中。图3d中单个颗粒内部的层状CoNiCrAlY金属相区域很少,这种微观结构的形成主要是由于机械合金化过程中CoNiCrAlY韧性相的塑性变形和ZrB2脆性相的破碎所致。在机械合金化过程中,脆性相ZrB2颗粒不会发生塑性变形,其直接破碎并嵌入CoNiCrAlY金属相中,形成CoNiCrAlY-ZrB2复合粉末。
图3
图3
一步式30 h和分步式35 h复合粉末的截面SEM像和EDS元素分布图
Fig.3
Low magnified cross-section SEM images (a, c) and high magnified cross-section SEM images and EDS analyses (b, d) of composite powders by 30 h one-step mechanical alloying (a, b), and 35 h step-fashion mechanical alloying (c, d)
上述研究表明,采用一步式和分步式MA工艺均可获得粉末粒度符合HVOF喷涂要求的CoNiCrAlY-20%ZrB2复合粉末,但分步式复合粉末中硬质相的分布更加均匀。因此,本工作选择MA-1工艺球磨30 h的复合粉末以及MA-2工艺球磨35 h的复合粉末作为后续喷涂的原始粉末,并对比研究2种涂层的组织和性能。
2.2 CoNiCrAlY-ZrB2 复合涂层的物相组成及微观结构
图4显示了HVOF制备的纯CoNiCrAlY涂层与2种CoNiCrAlY-ZrB2复合涂层的XRD谱。其中纯CoNiCrAlY涂层的衍射峰为金属相γ-(Co, Ni, Cr)固溶体。而采用机械合金化粉末制备的涂层增加了2个衍射峰,分别为β-NiAl金属间化合物和ZrB2陶瓷相,且γ相峰强度变低,峰窄而尖锐,表明涂层具有良好的晶体结构[14]。CoNiCrAlY-ZrB2复合涂层未发生明显氧化,依然可以看到明显的γ相衍射峰,而β-NiAl峰的形成在很大程度上被抑制。这是由于在严重塑性变形下,γ相拥有比β相更稳定的晶体结构[15],并且β相可以在机械合金化期间溶解成γ相[16,17]。XRD结果表明,低火焰温度和短停留时间的HVOF技术适用于制备CoNiCrAlY-ZrB2涂层。
图4
图4
CoNiCrAlY、MA-1及MA-2涂层的XRD谱
Fig.4
XRD spectra of CoNiCrAlY, MA-1, and MA-2 coatings
图5为CoNiCrAlY涂层和2种CoNiCrAlY-ZrB2复合涂层的表面及截面形貌。其中CoNiCrAlY涂层表面存在部分未充分熔化的半球形CoNiCrAlY合金颗粒,但是涂层本身致密均匀且孔隙较低,如图5a和b所示。MA-1粉末制备的CoNiCrAlY-ZrB2复合涂层(记为MA-1涂层)表面铺展良好,复合粉末充分熔化并沉积,仅观察到少量半熔化颗粒。由图5c和d可知,MA-1涂层截面的白色点状区域为ZrB2陶瓷颗粒,涂层与基体结合良好,但存在的孔隙较多。与MA-1涂层相比,MA-2粉末制备的CoNiCrAlY-ZrB2复合涂层(记为MA-2涂层)表面更加平整,但仍含有少量未完全熔化的颗粒。此外,MA-2涂层中ZrB2陶瓷颗粒均匀分布在CoNiCrAlY金属相中,涂层致密性更好,在涂层与基体界面处没有明显的孔隙,如图5e和f所示。在相同的HVOF喷涂参数下,采用MA-2复合粉末制备的CoNiCrAlY-ZrB2涂层比MA-1复合粉末的沉积效果更好,这可以归结为以下原因:(1) MA-2粉末的机械合金化程度更高,ZrB2陶瓷颗粒的分布更加均匀,使得复合涂层内部ZrB2分布同样更加均匀;(2) MA-2粉末球磨时间较MA-1粉末更久,复合颗粒表面形貌更加不规则、比表面积更大,因此在HVOF喷涂过程中,可以获得更好的加速与熔化效果。
图5
图5
不同涂层喷涂态的表面形貌及截面形貌
Fig.5
Surfacial (a, c, e) and cross-sectional (b, d, f) morphologies of different coatings
(a, b) CoNiCrAlY coating (c, d) MA-1 coating (e, f) MA-2 coating
图6a和b显示了MA-2涂层的TEM像。图6c和d分别为图6b中方形及圆形框的高分辨TEM(HRTEM)像和相应的快速Fourier变换(FFT),以及2个区域的选区电子衍射(SAED)花样分析。结果表明,其FFT图(图6c)证实了γ-(Co, Ni, Cr)固溶体的存在,图6d中的HRTEM像及其FFT验证了ZrB2陶瓷相的存在。TEM结果与XRD (图4)物相检测一致。从TEM-EDS结果(图6e)可以看出,ZrB2在涂层中均匀分布。此外,大多数ZrB2颗粒的尺寸小于100 nm,这表明采用分步式机械合金化造粉工艺及HVOF喷涂工艺制备的复合涂层具有纳米颗粒增强结构,纳米级ZrB2增强相均匀地分散在复合涂层中。
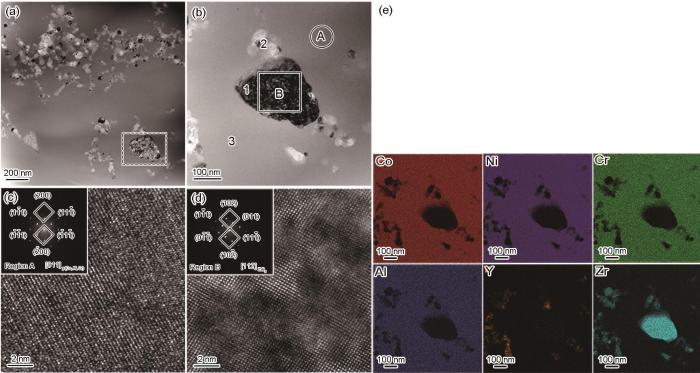
图6 MA-2涂层的TEM像、HRTEM像及选区电子衍射花样和EDS结果
Fig.6
Point | Mass fraction / % | ||||||
---|---|---|---|---|---|---|---|
Co | Ni | Cr | Al | Y | Zr | B | |
1 | 1.45 | 0.83 | 0.52 | 0.30 | - | 56.51 | 38.26 |
2 | 1.39 | 0.92 | 0.85 | 1.59 | 4.56 | 33.96 | 10.44 |
3 | 29.37 | 24.78 | 15.81 | 6.73 | 0.35 | 4.23 | 8.14 |
(a) bright-field image of coating (b) bright-field image of ZrB2
(c, d) HRTEM images and SAED patterns (insets) of region A (c) and region B (d)
(e) EDS results of region B
2.3 CoNiCrAlY-ZrB2 复合涂层的力学性能
表2显示了CoNiCrAlY涂层和2种CoNiCrAlY-ZrB2复合涂层的孔隙率、显微硬度、断裂韧性及结合强度。其中,纯CoNiCrAlY涂层的孔隙率仅为0.17%,而MA-1和MA-2涂层的孔隙率分别为0.36%和0.28%。MA-1和MA-2涂层的硬度均远高于HVOF喷涂NiCoCrAlY涂层(450 HV0.1)[18]和激光熔覆NiCoCrA1Y涂层(350.5 HV0.1)[19],这主要是由于Co含量的增加以及纳米ZrB2颗粒的添加。此外,MA-1涂层的显微硬度(672 HV0.3)略低于MA-2涂层(738 HV0.3),这表明ZrB2的均匀分布有助于提高HVOF涂层的显微强度。MA-2涂层的断裂韧性(5.21 MPa·m1/2)较MA-1涂层提高了11%,表明MA-2涂层具有更好的阻碍裂纹扩展的能力。结合强度测试结果表明,MA-1涂层和MA-2涂层均是胶断,涂层内部未发生断裂,结合强度大于70 MPa,而CoNiCrAlY涂层的结合强度仅为45.8 MPa。陶瓷第二相的引入会导致孔隙、裂纹的增加,使得CoNiCrAlY-ZrB2复合涂层的孔隙率高于CoNiCrAlY涂层。但是纳米ZrB2硬质陶瓷相分布于复合涂层的内部起到弥散强化的作用,导致MA-1和MA-2涂层的显微硬度和断裂韧性要高于CoNiCrAlY涂层,且陶瓷相分布更加均匀的MA-2涂层对应的性能更好。此外,不规则的机械合金化颗粒比球形的合金颗粒在超音速火焰中拥有更好的加速和熔化效果,使得沉积的涂层更倾向于冶金结合,从而提高了MA-1和MA-2涂层的结合强度。
表2 3种涂层的孔隙率、显微硬度、断裂韧性及结合强度
Table 2
Coating | Porosity / % | Hardness / HV0.3 | KIC / (MPa·m1/2) | Bonding strength / MPa |
---|---|---|---|---|
CoNiCrAlY | 0.17 | 573 | 2.36 | 45.8 |
MA-1 | 0.36 | 672 | 4.69 | > 70 |
MA-2 | 0.28 | 738 | 5.21 | > 70 |
2.4 复合涂层的高温摩擦磨损性能
CoNiCrAlY涂层及MA-1、MA-2复合涂层在不同温度下的摩擦系数(COF)随磨损时间的变化曲线如图7所示。3种涂层的摩擦系数随测试温度具有相似的变化趋势,即先上升后下降,在950 ℃时最低。此外,CoNiCrAlY涂层在550和750 ℃时的COF要高于2组CoNiCrAlY-ZrB2复合涂层,分别为0.64和0.69。当温度达到950 ℃时其平均摩擦系数为0.41。
图7
图7
3种涂层在不同温度下的摩擦系数(COF)曲线
Fig.7
Coefficient of friction (COF) curves at different temperatures of CoNiCrAlY (a), MA-1 (b), and MA-2 (c) coatings (t—time)
对比2组CoNiCrAlY-ZrB2复合涂层可见,在中低温环境下(550和750 ℃),MA-1涂层与MA-2涂层的COF差异性较小。随着磨损时间的增加,550和750 ℃时MA-1涂层的COF分别稳定在0.62和0.68左右,MA-2涂层的COF分别稳定在0.61和0.66左右。相较于550 ℃,750 ℃条件下2种涂层COF的升高可以归结为以下2个原因:(1) 涂层表面随着温度的升高而软化;(2) 在与磨球滑动的过程中,一些ZrB2硬质颗粒被拉出并困在金属相中,从而在一定程度上阻碍了摩擦副的相对运动,增加了COF。950 ℃时MA-1涂层的COF稳定在0.39左右,MA-2涂层的平均摩擦系数为0.36。即随着温度的升高,2种涂层表面均呈现出一种润滑、减摩的效果,且MA-2涂层的润滑、减摩效果更加突出。在3个测试温度下,MA-1涂层的平均摩擦系数均高于MA-2涂层,这可能是由于MA-2涂层中纳米ZrB2分布更加均匀造成的。
图8给出了不同测试温度下3种涂层的磨损率和平均摩擦系数。图9给出了3种涂层磨损痕迹的2D形貌。结果表明,MA-1涂层和MA-2涂层的磨损率变化趋势无明显差异。随着温度的升高,2种涂层的磨损率随着温度升高先增大后显著降低。计算结果表明,MA-1涂层在550、750和950 ℃时的磨损率分别为2.23 × 10-13、5.01 × 10-13和4.28 × 10-14 m3/(N·m),而MA-2涂层在550、750和950 ℃时的磨损率分别为1.95 × 10-13、4.39 × 10-13和1.71 × 10-14 m3/(N·m)。纳米ZrB2增强相的均匀分布可以大大提高涂层在高温环境下的耐磨性,且在950 ℃时MA-2涂层的耐磨性较MA-1涂层提高了60%。与复合涂层磨损率变化趋势不同,相较于中低温环境(550和750 ℃),950 ℃时CoNiCrAlY涂层的磨损率显著升高,达到7.79 × 10-13 m3/(N·m),分别是MA-1涂层和MA-2涂层的18和46倍。这表明ZrB2陶瓷颗粒加入对涂层高温摩擦磨损性能提升明显,且更均匀的陶瓷相分布可以获得更佳的性能。
图8
图8
3种涂层在不同温度下的平均COF和磨损率
Fig.8
Average COFs and wear rates of the three coatings at different temperatures
图9
图9
3种涂层磨痕的2D形貌
Fig.9
2D morphologies of worn tracks of CoNiCrAlY (a), MA-1 (b), and MA-2 (c) coatings
CoNiCrAlY涂层、MA-1涂层和MA-2涂层在不同温度摩擦磨损后磨痕形貌的SEM像和EDS结果如图10~12和表3~5所示。在550和750 ℃时,结合相应的EDS可以看出,3种涂层表面均未发生明显的氧化,磨痕表面仅存在沿滑动方向上的不连续带状犁沟和黏着断裂(图10a~d、11a~d和12a~d),展现出典型的黏着磨损和磨粒磨损特征,且以磨粒磨损为主要磨损机制。值得注意的是,由于CoNiCrAlY涂层没有硬质陶瓷相的存在,其硬度更低,在与Si3N4磨球接触时更倾向于被切削出现分层现象,如图10a和b所示。对于MA-1涂层和MA-2涂层,在550和750 ℃时,ZrB2陶瓷颗粒的添加并没有给涂层带来良好的耐磨损性能,这是由于涂层与Si3N4磨球滑动期间,CoNiCrAlY金属相中的ZrB2颗粒阻碍了摩擦副的相对运动,导致2种涂层的耐磨性能均不理想。但当温度达到950 ℃时,复合涂层表面均发生了明显的氧化,磨损表面氧化物保护膜主要由Al、Co、Cr、Zr等的氧化物组成(图11e、f和图12e、f)。这些氧化物膜连接成层并黏附在涂层表面,形成“上釉层”,从而使涂层具有自润滑能力,且纳米ZrB2的存在可以有效缓解高温软化造成的硬度下降,使得950 ℃时CoNiCrA1Y-ZrB2复合涂层的磨损率大幅降低[3,20~23]。同时,涂层的磨损机制也从中低温(550~750 ℃)的黏着磨损和磨粒磨损转变成高温条件下(950 ℃)的氧化磨损。
图10
图10
不同温度下CoNiCrA1Y涂层的磨损表面形貌SEM像
Fig.10
Low (a, c, e) and high (b, d, f) magnified SEM images of worn surface morphologies of the CoNiCrA1Y coatings at different temperatures
(a, b) 550 oC (c, d) 750 oC (e, f) 950 oC
表3 不同温度下CoNiCrA1Y涂层磨损表面的EDS分析 (mass fraction / %)
Table 3
Point | Co | Ni | Cr | Al | Zr | O |
---|---|---|---|---|---|---|
1 | 26.54 | 22.73 | 14.81 | 6.69 | 1.20 | 28.03 |
2 | 29.42 | 25.00 | 16.43 | 5.53 | 1.09 | 22.54 |
3 | 29.35 | 23.23 | 17.32 | 6.63 | 0.67 | 22.81 |
4 | 34.98 | 32.62 | 19.19 | 10.20 | 0.43 | 2.58 |
5 | 20.80 | 12.44 | 14.44 | 25.75 | 0.20 | 26.37 |
6 | 14.85 | 8.06 | 11.15 | 35.19 | 0.42 | 30.32 |
表4 不同温度下MA-1涂层磨损表面的EDS分析 (in Fig.11)(mass fraction / %)
Table 4
Point | Co | Ni | Cr | Al | Zr | O |
---|---|---|---|---|---|---|
1 | 19.14 | 20.11 | 9.68 | 7.72 | 6.24 | 37.10 |
2 | 37.09 | 30.84 | 20.21 | 8.74 | 3.13 | - |
3 | 23.26 | 20.30 | 12.92 | 6.60 | 8.50 | 28.44 |
4 | 35.01 | 26.59 | 18.97 | 6.82 | 9.32 | 3.29 |
5 | 20.68 | 17.23 | 11.74 | 3.89 | 7.96 | 18.12 |
6 | 25.04 | 12.05 | 30.24 | 7.27 | 4.10 | 21.30 |
表5 不同温度下MA-2涂层磨损表面的EDS分析 (mass fraction / %)
Table 5
Point | Co | Ni | Cr | Al | Zr | O |
---|---|---|---|---|---|---|
1 | 21.19 | 18.06 | 11.68 | 5.72 | 9.24 | 34.10 |
2 | 21.64 | 18.34 | 13.25 | 6.17 | 11.18 | 29.42 |
3 | 12.47 | 9.70 | 9.52 | 3.38 | 28.55 | 36.38 |
4 | 40.13 | 30.29 | 21.41 | 8.17 | - | - |
5 | 19.50 | 16.34 | 10.66 | 5.05 | 8.20 | 30.06 |
6 | 22.94 | 11.55 | 28.64 | 5.87 | 6.20 | 24.80 |
图11
图11
不同温度下MA-1涂层的磨损表面形貌SEM像
Fig.11
Low (a, c, e) and high (b, d, f) magnified SEM images of worn surface morphologies of the MA-1 coatings at different temperatures
(a, b) 550 oC (c, d) 750 oC (e, f) 950 oC
图12
图12
不同温度下MA-2涂层的磨损表面形貌SEM像
Fig.12
Low (a, c, e) and high (b, d, f) magnified SEM images of worn surface morphologies of the MA-2 coating at different temperatures
(a, b) 550 oC (c, d) 750 oC (e, f) 950 oC
为了进一步分析复合涂层高温摩擦磨损性能的变化机制,将MA-2涂层与纯CoNiCrAlY涂层进行了对比分析。图13为CoNiCrAlY涂层和MA-2涂层在不同温度摩擦磨损后磨痕的Raman光谱分析结果。可以看出,在低于750 ℃时CoNiCrAlY涂层磨损表面产生了Co3O4、Cr2O3和CoO相,950 ℃的磨损表面检测到了Al2O3相,这主要是由于摩擦过程中化学反应引起的碎片氧化。研究[21~23]表明,当氧化物碎片的含量达到一定水平时,这些氧化物碎片混合、破碎成小颗粒,最后通过烧结反应黏附在磨损表面上,形成“上釉层”。而MA-2涂层的磨损表面除了这些物相,还检测到了CoCr2O4和m-ZrO2相。氧化物含量的增加,有助于促进烧结反应的增强,使得生成的“上釉层”更加连续、完整,且CoCr2O4作为一种很好的固体润滑剂[3],能够提供更好的“釉”,这也解释了950 ℃时复合涂层摩擦系数和磨损率大幅度降低的原因。
图13
图13
不同温度下涂层摩擦磨损后磨痕的Raman光谱
Fig.13
Raman spectra of worn surface at different temperatures
(a) CoNiCrAlY coating (b) MA-2 coating
表6给出了CoNiCrAlY-ZrB2涂层与其他文献报道[2,5,19,24,25]的同类涂层体系的磨损率对比。现有的报道中大多为800 ℃以下的高温摩擦磨损实验,缺乏对涂层在更高温度(如950 ℃)的研究[3]。与本工作的CoNiCrAlY-ZrB2涂层磨损率(950 ℃)相比,600 ℃的CoCrAlYTa-10%Al2O3涂层磨损率(1.5 × 10-14 m3/(N·m))[24]和700 ℃的NiCrAlY-Al2O3涂层磨损率(2 × 10-14 m3/(N·m))略低[2]。而800 ℃的NiCoCrAlY-Al2O3涂层(9.6 × 10-14 m3/(N·m))[5]、700 ℃的CoCrAlYTaSi-Al2O3涂层(3 × 10-14 m3/(N·m))[25]和500 ℃的NiCoCrAlY-Al2O3/SiC/CeO2涂层(1.02 × 10-13/0.60 × 10-13/1.14 × 10-13 m3/(N·m))[19]的磨损率更高。这表明,本工作中的纳米ZrB2颗粒增强CoNiCrAlY复合涂层作为高温炉辊的保护涂层具有很大的应用潜力。
表6 本工作与其他文献报道[2,5,19,24,25]的COF和磨损率比较
Table 6
3 结论
(1) 采用一步式和分步式机械合金化工艺可以制备出纳米ZrB2增强的CoNiCrAlY复合粉末,且分步式复合粉末内部ZrB2颗粒比一步式分布得更加均匀,机械合金化效果更好。复合粉末的粒径随着球磨时间的增加而减小,30和35 h分别是一步式和分步式机械合金化的最佳球磨时间,平均粒径分别为39.5和38.6 μm。
(2) 采用HVOF可以制备出致密性高、组织均匀的CoNiCrAlY涂层和CoNiCrAlY-ZrB2复合涂层。复合涂层主要包含γ-(Co, Ni, Cr)、β-NiAl和ZrB2 3种物相。与CoNiCrAlY涂层相比,纳米ZrB2的加入使得一步式和分步式复合涂层的硬度、断裂韧性、结合强度明显提升。其中分步式复合涂层拥有最高的显微硬度(738 HV0.3)和断裂韧性(5.21 MPa·m1/2)。
(3) 纳米ZrB2颗粒的加入可以显著提升涂层的高温摩擦磨损性能。由于在Si3N4磨球摩擦过程中形成了“上釉层”,MA-1和MA-2复合涂层在950 ℃高温下均具有良好的自润滑能力,2者的平均摩擦系数分别为0.39和0.36。MA-2涂层具有更好的高温耐磨性能,且950 ℃时的磨损率仅为1.71 × 10-14 m3/(N·m),比MA-1涂层低了60%。CoNiCrAlY-ZrB2复合涂层的磨损机理随温度变化,550和750 ℃时存在磨粒磨损和黏着磨损,且以磨粒磨损为主,950 ℃时的磨损机理主要是氧化磨损。
参考文献
Review of thermal spray coating applications in the steel industry: Part 1—Hardware in steel making to the continuous annealing process
[J].
Tribology of NiCrAlY + Al2O3 composite coatings by plasma spraying with hybrid feeding of dry powder + suspension
[J].
Effect of alumina dispersion on oxidation behavior as well as friction and wear behavior of HVOF-sprayed CoCrAlYTaCSi coating at elevated temperature up to 1000 oC
[J].
Development of alloyed and dispersion-strengthened MCrAlY coatings
[J].
Wear behaviour of Al2O3 dispersion strengthened MCrAlY coating
[J].
Review on nanocomposites fabricated by mechanical alloying
[J].
Nanostructured materials and nanocomposites by mechanical alloying: An overview
[J].The technique of mechanical alloying, although originally developed to produce oxide-dispersion-strengthened superalloys for aerospace and high-temperature applications, is now recognized as an important and versatile technique to synthesize metastable and advanced materials with a high potential for widespread applications. Mechanical alloying involves repeated cold welding, fracturing, and rewelding of powder particles in a high-energy ball mill. The reduced diffusion distances between metal powder layers formed as a result of heavy deformation, introduction of a high density of crystal defects, and a slight rise in powder temperature contribute to alloy formation from blended elemental powders. The type of phases/materials produced by mechanical alloying of powder mixtures include supersaturated solid solutions, intermetallics, quasicrystalline alloys, high-entropy alloys, amorphous alloys, and composites. If the material produced is crystalline in nature, most often the grain size is in the nanometer size. Amongst these phases, nanostructured materials and nanocomposites have been the most important types investigated. In this contribution, we will present an overview of the processing, characteristics, and properties of nanocrystalline materials and nanocomposites produced by mechanical alloying, with special emphasis on our recent work.
High-temperature oxidation behavior of spark plasma sintered Ni20Cr-xAl alloys
[J].
放电等离子烧结Ni20Cr-xAl合金的高温氧化行为
[J].高温氧化是限制镍基高温合金服役寿命的主要因素之一。本工作旨在通过调控Al含量来提升Ni20Cr合金的抗氧化性能。采用机械合金化(MA)和放电等离子烧结(SPS)的方法制备了Al含量(质量分数)分别为1.5%、3.0%、5.0%的Ni20Cr-xAl合金,对比研究了SPS制备合金与相同成分铸态合金在900℃空气中的高温氧化行为。结果表明,SPS制备合金成分、组织均匀且晶粒细小,大量晶界显著加速了元素的扩散,在Al含量为1.5%时,Al内氧化严重,Cr快速外氧化生成含有大量孔隙和裂纹的Cr<sub>2</sub>O<sub>3</sub>膜,而在Al含量为3.0%和5.0%时,形成了保护性的连续致密的α-Al<sub>2</sub>O<sub>3</sub>薄膜,合金内部弥散的Al<sub>2</sub>O<sub>3</sub>颗粒为外Al<sub>2</sub>O<sub>3</sub>膜提供了形核位点并起到了钉扎作用,因此2者表现出优异的抗氧化性能,氧化速率分别为1.06 × 10<sup>-7</sup>和4.92 × 10<sup>-8</sup> mg<sup>2</sup>/(cm<sup>4</sup>·s)。铸态合金都发生了内氧化,而且无法形成连续的外Al<sub>2</sub>O<sub>3</sub>膜,氧化膜的主要成分为疏松多孔的Cr<sub>2</sub>O<sub>3</sub>,因而氧化速率快且发生了氧化膜开裂和剥落。
Microstructure and mechanical properties of carbon nanotubes-reinforced 7055Al composites fabricated by high-energy ball milling and powder metallurgy processing
[J].In the recent years, lightweight and high-strength structural materials have gained much attention in engineering applications. Carbon nanotube (CNT)-reinforced Al (CNT/Al) composites are promising structural materials owing to the good mechanical properties and high reinforcing efficiency of CNTs. Previous studies on these composites mainly focused on fabricating CNT-reinforced low-strength or medium-high-strength Al alloys (such as pure Al, or 2xxx series or 6xxx series Al alloys) composites via various dispersion methods. However, only few studies investigated composites with super-high-strength Al alloys as the matrices. In the present work, CNT/7055Al composites with CNT volume fractions of 0%, 1%, and 3% were prepared by high-energy ball milling combined with powder metallurgy. The CNT distribution, grain structure, interface, and mechanical properties of the CNT/7055Al composite were investigated using OM, SEM, TEM, and tensile tests. The strengthening mechanism and anisotropy of the composite were analyzed. The results indicated that the composite had a bimodal grain structure consisting of CNT-free coarse grain zones and CNT-enriched ultrafine grain zones. CNTs were well dispersed in the ultrafine grain zones of the Al matrix, and the CNT/Al interface was clean. There were only few reaction products at the interface. The tensile strength of the 3%CNT/7055Al composite reached 816 MPa, but the elongation was only 0.5%. Grain refinement and Orowan strengthening were the main strengthening mechanisms of the CNT/7055Al composite. Because of the load transfer efficiency of CNTs and a coarse grain band structure, the composite exhibited stronger anisotropy than the matrix alloy. The tensile properties of the CNT/7055Al composite normal to the extrusion direction were weaker than those in the extrusion direction.
高能球磨结合粉末冶金法制备碳纳米管增强7055Al复合材料的微观组织和力学性能
[J].
Fabrication and properties of titanium-hydroxyapatite nanocomposites
[J].
Effect of CeO2 on corrosion behavior of WC-12Co coatings by high velocity oxygen fuel
[J].
CeO2对超音速火焰喷涂WC-12Co涂层腐蚀行为的影响
[J].采用超音速火焰喷涂在Q345基体上制备了微米WC-12Co, 纳米改性WC-12Co和CeO<sub>2</sub>改性WC-12Co涂层, 利用SEM, XRD和显微硬度计等手段观察表征了涂层的微观组织、相成分和显微硬度, 通过LSCM, SEM, 极化实验和浸泡腐蚀实验等方法研究分析了涂层在1 mol/L H<sub>2</sub>SO<sub>4</sub>溶液中的腐蚀行为和腐蚀机理. 结果表明: 纳米CeO<sub>2</sub>的加入可以显著降低涂层的孔隙率, 有效减少局部腐蚀的发生; 同时添加纳米CeO<sub>2</sub>可以使涂层电极电位发生正移, 降低腐蚀电流密度, 生成稳定的钝化膜, 降低涂层的维钝电流密度, 提高涂层的耐腐蚀性能; 纳米CeO<sub>2</sub>改性WC-12Co涂层的腐蚀机制为由孔隙诱发的局部腐蚀, 孔隙处的Co黏结相不断被腐蚀导致WC颗粒失去了支撑作用而脱落, 从而露出新的Co黏结相, 促进了涂层的腐蚀, 使孔隙不断扩大形成腐蚀坑. 而微米WC-12Co涂层和纳米改性WC-12Co涂层不仅最外层的Co黏结相被腐蚀, 而且在孔隙处也发生了严重的局部腐蚀.
Microstructure and high-temperature friction and wear behavior of WC-(W, Cr)2C-Ni coating prepared by high velocity oxy-fuel spraying
[J].
Influence of particle size distribution on the morphology and cavitation resistance of high-velocity oxygen fuel coatings
[J].
Microstructure and thermal stability of MoSi2-CoNiCrAlY nanocomposite feedstock prepared by high energy ball milling
[J].
CoNiCrAlY microstructural changes induced during cold gas dynamic spraying
[J].
Microstructural and morphological evaluation of MCrAlY/YSZ composite produced by mechanical alloying method
[J].
Microstructural and high-temperature cyclic oxidation response of NiCoCrAlY coatings with and without SiC + ZrB2 reactive-element dispenser
[J].
Development of oxide dispersion strengthened MCrAlY coatings
[J].
High temperature frictional wear behaviors of nano-particle reinforced NiCoCrAlY cladded coatings
[J].
Experimental study of indentation fracture toughness in HVOF sprayed hardmetal coatings
[J].
Investigation into the wear behaviour of Stellite 6 during rotation as an unlubricated bearing at 600 oC
[J].
Studies of high temperature sliding wear of metallic dissimilar interfaces Ⅱ: Incoloy MA956 versus Stellite 6
[J].
Investigation into the wear behaviour of Tribaloy 400 oC during rotation as an unlubricated bearing at 600 oC
[J].
Effects of temperature on wear properties and mechanisms of HVOF sprayed CoCrAlYTa-10%Al2O3 coatings and H13 steel
[J].
Influence of Al2O3 mass fractions on microstructure, oxidation resistance and friction-wear behaviors of CoCrAlYTaSi coatings
[J].
/
〈 |
|
〉 |
