作者简介: 吴宣楠, 男, 1989 年生, 硕士
针对穿孔等离子弧焊接工艺, 建立了定点焊的二维轴对称非稳态数理模型, 描述高温流动的电弧与工件熔池的耦合输运过程, 通过数值模拟获得了电场、磁场、流场与温度场的演变规律. 模拟焊缝熔合线与实验结果吻合较好, 验证了数学模型的合理性. 研究结果表明: W阴极尖端附近的电流密度与温度是最高的; 等离子弧在工件上部呈现出“钟形”, 而在中心轴线处因进入小孔呈细长的“锥形”; 高速Ar气等离子体冲击到小孔壁面时速度急剧降低, 小孔内出现高压区和Ar气等离子体的返流现象; 熔池内流动与传热的综合作用使焊缝熔合线呈倒“喇叭形”. 进一步对焊接的操作参数及焊枪结构参数进行了影响因素的正交试验模拟. 极差分析表明, 焊枪的结构因素比焊接操作参数更重要, 即对电极间距、电极内缩量、喷嘴孔径需予以重点考虑, 以获得良好的焊缝形状.
A 2D axial symmetrical mathematical model was developed for stationary keyholing plasma arc welding (PAW), to describe the transport process in coupled high-temperature flow arc and molten pool in the workpiece. The evolutions of electric, magnetic, velocity and temperature fields were simulated. The simulated fusion line of the weld bead is in quite good agreement with the experimental results, validating the mathematical model. It turns out that, both the current density and the temperature reach the maximum values near the tip of the tungsten cathode. The arc displays a typical bell-shape above the workpiece, but becomes slim cone-shape near the central axis as the arc enters the keyhole. The argon plasma slows down sharply when it strikes the inner wall of the keyhole, so high pressure appears in the keyhole and some argon plasma flows back. The combination of fluid flow and heat transfer contributes to the reversed bugle shaped fusion line. The simulation of orthogonal test was further conducted to study the effects of operational and structural parameters of the weld torch. The range analysis shows that the structural parameters of weld torch are more influential than the operational parameters. That is, more attention should be paid to control the gap between two electrodes, the electrode shrinkage and the nozzle diameter to guarantee the welding quality.
在高速发展的现代加工制造业中, 焊接已经渗透到其中的各个领域. 随着科学技术的进步, 产品装备对轻量化、节能化、高参量化要求日益提高, 这对焊接新工艺和新技术提出了越来越高的要求. 在当前最先进的3种高能束流[1]焊接中, 尽管电子束焊与激光焊在精密焊接及能量控制等方面具有一定的优越性, 但是它们设备复杂并且价格昂贵, 同时操作要求较高, 不适合大规模焊接生产. 而等离子弧焊接(plasma arc welding, PAW)设备造价及运行成本较低, 焊接的操作过程相对简单, 因而被人们极大地关注. PAW的能量密度可达105~106 W/cm2, 其电弧的最高温度可达52000 K[2]. 在焊接过程中, PAW对工件的变形影响小, 工件残余应力小, 焊接成型的几率比较大, 焊缝深宽比大[2]. 尤其是小孔型PAW, 它使普通PAW方法的导热焊转变为穿孔焊, 加深了传热深度, 极大地改善了焊缝附近热量分布和利用, 能够形成很大的焊接深度和很小的热影响区. 因此, 小孔型PAW热量集中, 熔透力强, 焊接速度快, 可以实现单面焊双面成型, 能够进行10 mm以下壁厚材料的无坡口对焊连接. 然而, 小孔型PAW也有许多关键问题尚待解决, 如小孔对焊接工艺条件的变化比较敏感; 焊缝成型的稳定性较差; 获得良好焊接质量的合理规范参数区间窄等[3,4]. 因此, 近年来穿孔PAW相关的研究工作受到了广泛重视.
针对电弧部分, Tashiro等[5]建立了中空阴极弧(hollow cathode arc, HCA)模型来研究不同工况下Ar气的热源特性, 发现HCA焊接比W极气体保护电弧焊(gas tungsten arc welding, GTAW)对工件的加热更加均匀. Aithal等[6]建立二维PAW模型, 模拟等离子体在焊枪内的层流流动以及向工件表面的喷射过程, 用工件表面上的滞止压强分布来验证模型的可靠性, 但是没有考虑热辐射. Tashiro等[7]研究了当弧长变化时焊接的电源特性对弧温度与弧功率的影响作用.
针对PAW熔池的传热现象, 人们开展了大量的研究[8,9,10,11,12], 但往往忽略了熔池的流动及穿孔. 为研究熔池中的穿孔行为, 王小杰等[3]利用Level-Set方法追踪了定点焊小孔界面的演变过程, 模拟实现了工件的穿孔, 然而该模型中电弧向工件传递的热量以及熔池中气-液界面两侧气相与液相的流体速度都是通过既定表达式给定的, 没有考虑电弧对工件熔池的热力作用. 张涛等[13]采用焓-孔隙度法处理相变潜热与动量损耗问题, 并用流体体积函数(volume of fluid, VOF)法追踪小孔界面. 霍玉双等[4]使用“双椭球体+峰值热流递增的圆柱体”的组合式体积热源模型来确定熔池的形状与尺寸, 再在此基础上通过熔池内部的受力分析建立小孔的形状方程, 最终确定了小孔的形状. 孙俊华等[14]采用“双椭球+锥体”组合式体积热源模型以及焊接熔池的表面变形方程, 研究小孔形状随受控脉冲电流的动态变化过程, 实现了小孔的“打开”与“闭合”. Li等[15]提出复合体积热源模型, 由双椭球热源和圆锥体热源组成, 它能兼顾热效应和小孔效应, 很好地模拟再现了焊缝熔合线的驼峰. 但以上研究都未考虑等离子弧的实际作用, 是用简化的等效热源模型来描述等离子弧提供的能量和穿孔效应.
基于等离子弧与熔池的耦合模拟, Yamamoto等[16]研究金属蒸发对电弧及熔池的影响. Tashiro等[17]建立了考虑熔池中流动的弧与熔池的耦合模型, 通过预设圆柱形小孔直径获得表面张力、蒸汽压力、切应力随小孔直径的变化规律曲线, 最终由三力平衡确定了稳定状态下的小孔直径. Tanaka等[18]建立了二维轴对称模型, 研究弧与熔池的传热流动对焊缝几何的影响, 研究表明, 熔池的流动由电弧拖拽力、电磁力、浮升力、Marangoni力引起, 相比而言, 电弧拖拽力与Marangoni力起支配作用, 二者的平衡决定了熔池中的环流方向.
综上所述, 尽管对PAW的模拟研究很多, 但多是对工件及熔池单独进行的, 无法真实再现高温高速等离子弧对熔池复杂的热力作用; 在弧与熔池耦合的研究中, 几乎都未考虑等离子弧对工件的穿通孔作用, 也未考虑熔池的流动, 影响了对熔池中流动相变传热机理的准确认识. 因此, 本工作拟建立定点PAW中等离子弧与熔池耦合的二维轴对称数学模型, 分析电弧及熔池中的电场、磁场、流场、温度场的演变规律及相互作用; 将焊缝熔合线模拟结果与实验数据进行对比, 以验证本工作模型的可靠性; 并进一步对焊接的结构参数、操作参数进行正交试验设计, 通过模拟和极差分析确定各影响因素的主次关系, 以期为实际穿孔PAW工艺优化提供指导.
图1是穿孔PAW示意图. 等离子弧焊枪的W阴极和工件分别连接于电源的两极, 通电后在W阴极和工件之间产生电流, 由于电流的Joule热作用使Ar气被加热电离形成等离子体, 产生了电弧. 电弧燃烧于W阴极和工件之间, 连续送入的工作气体穿过电弧空间之后成为从喷嘴喷出的高温等离子焰流. 电弧经过机械压缩、热压缩、电磁收缩这3种压缩效应后, 能量高度集中在直径很小的弧柱中[2]. 弧柱压缩程度较强, 等离子焰流喷出速度较大, 因此, 压缩电弧能量集中, 穿透力很强, 可以用于金属材料的高效快速焊接.
穿孔PAW几何模型如图2所示, AB为W阴极尖端, 电极内缩2 mm, 工作气体从水冷喷嘴的入口CD处喷入, 保护气体从保护气喷嘴的入口GH处喷入. 由于焊接过程受到一系列物理因素的复杂作用, 为突出问题本质, 建立合理的模型, 本工作引入以下假设条件[19,20]: (1) 等离子体光学薄, 且处于局部热力学平衡状态; (2) 等离子体的热导率、密度、黏度、定压比热容和电导率均是温度的函数; (3) 电弧中高温等离子体与熔池中液态金属流动均为层流、不可压缩Newton流体; (4) 预设一个贯穿工件的倒圆台型固定小孔, 其底部半径由实验数据[1]确定; 实验发现焊接稳定后小孔底部的尺寸变化较小[21,22], 将小孔底部半径根据实验数据取为定值0.5 mm[1]; (5) 工件中除了金属的热导率以及液态黏度与温度有关外, 其它热物性参数均为常数; (6) 熔池自由表面为平面无变形, 忽略其蒸发损失.
![]() | Fig.2 Geometric model of keyholing PAW (unit: mm, r—radial coordinate, z—axial coordinate)图2 穿孔PAW几何模型 |
基于以上假设, 建立了如下的等离子弧与熔池输运过程的二维轴对称数学模型.
质量守恒方程:
r方向动量守恒方程:

z方向动量守恒方程:
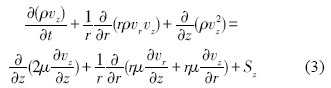
能量守恒方程:

电荷守恒方程:
Ohm定律:
磁矢量势方程:
式中, t是时间, s; r是密度, kg/m3; r和z分别为径向与轴向坐标, m; vr和vz分别为径向与轴向速度, m/s; m是动力黏度, kg/(ms); Sr和Sz分别为径向与轴向动量守恒方程源项, N/m3; cp是比热容, J/(kgK); T是热力学温度, K; k是热导率, W/(mK); Se是能量守恒方程源项, W/m3; s是电导率, S/m;
采用焓-多孔技术[23]处理工件熔化过程的相变. 材料总焓值被定义为显焓与潜热的总和, 即:
![]() | Table 1 Source items in momentum and energy equations 表1 动量与能量守恒方程的源项 |
![]() | Fig.3 Temperature-dependent thermophyical properties of Ar plasma[34](a) density and dynamic viscosity(b) specific heat(c) thermal conductivity and electrical conductivity图3 Ar气等离子体的热物性随温度变化曲线[34] |
式中, H是材料总焓值, J/kg; h是显焓, J/kg; La是熔化潜热, J/kg;
式中, Ts是304不锈钢的固相线温度, K; Tl是304不锈钢的液相线温度, K.
两相区(糊状区)被视为多孔介质, 考虑固/液相间的相互作用力, 根据Darcy定律[24]确定:
式中,
应用Kozeny-Carman表达式[23]计算该区域的渗透率K:
式中, D0是与多孔介质结构有关的系数, 根据文献[8,25], 模型中可取为常数1.2×1010.
考虑式(12)~(14), 在熔池动量守恒方程中加入如下源项, 以表征固/液相界面上的相间作用力:
式中, S是固/液相界面上的相间作用力, N/m3.
动量与能量守恒方程中的源项表达式见表1. 电弧动量守恒方程源项中主要有电磁力, 能量守恒方程的源项有Joule热、电子输运焓和辐射热损失. 磁矢量势微分控制方程及电荷守恒方程的求解正确, 是电弧中动量守恒方程中电磁力与能量守恒方程中Joule热正确加载的保证与前提. 磁场的求解采用磁矢量势微分控制方程, 避免了按照Ampere环路定理对电流密度进行复杂的积分计算磁场. 熔池动量守恒方程中考虑切应力、重力和Darcy阻力, 忽略电磁力[26].
辐射热损失R计算参考文献[27], 如式(16)所示:

本工作计算域如图2所示, 其中ABCDEFGHIMKLA为等离子体区域, IJKMI为工件区域. 模型计算条件如表2所示. 其中, n表示法向方向; LA是对称轴; AB是焊枪的电流入口; BC是焊枪电极壁面; DE, EF和FG是水冷Cu壁面; KL是小孔底部出口; HI是上部等离子体出口; CD和GH分别是工作气体和保护气体的速度入口, 且假设为等速分布; IJ和JK分别是工件侧表面和下表面, 其热边界条件如式(17)所示, 考虑了对流换热与辐射换热:
![]() | Table 2 Initial and boundary conditions 表 2 初始条件和边界条件 |
![]() | Fig.4 Distributions of electrical potential and current density in arc column and workpiece at 2.0 s图4 在2.0 s时刻弧柱及工件中电势与电流密度分布 |
式中, q是热流密度, W/m2; e是外部壁面辐射率; a是Stefan-Boltzmann常数, W/(m2K4); Tw是工件表面温度, K; T∞是环境温度, K; hd是表面对流换热系数, W/(m2K). T∞为300 K, hd的计算参考文献[28]:
MI和MK分别为工件上表面和小孔侧壁面. 由于焊接熔池表面温度分布不均匀, 表面张力随温度梯度变化产生Marangoni力[29](式(19)), 它对熔池的流动驱动起重要作用[8].
式中, tr和 tz分别为径向与轴向切应力, N/m2; g是表面张力, N/m, 它的数值由实验数据[30]给定.
本工作采用计算流体力学(CFD)软件FLUENT对数学模型进行求解. 采用非结构化网格对计算区域进行离散化, 靠近对称面处选用小尺寸密集网格, 远端区域选用大尺寸稀疏网格. 采用PISO算法求解离散的微分控制方程组, 其中动量守恒方程和能量守恒方程的对流项采用二阶迎风离散格式, 压力插值采用Standard格式. 数值计算收敛条件是连续性方程的绝对残差和小于10-3, 而能量方程绝对残差和小于10-6, 其余方程的绝对残差和均为小于10-4. 同时, 为避免假收敛现象, 还补充MI和MK界面上两侧总热流量绝对值的相对差值小于10-3作为能量方程的收敛判据. 时间步长设置为0.01 s.
根据现有研究[31,32,33], 等离子弧物性参数受温度影响很大, 本工作采用文献[34]给出的Ar气等离子体密度、比热容、黏度、热导率及电导率随温度的变化值, 如图3所示. 表3[8]给出了304不锈钢平板的物性参数与焊接工艺参数的数值.
实际工艺和模拟结果均表明电弧温度在整个过程中变化很小, 即在穿孔等离子弧定点焊接过程中电弧容易维持热稳定状态. 图4~7给出了2.0 s时刻弧柱及工件中各物理量的分布状态, 包括电场、电磁力场、温度场、流场与压力场.
![]() | Table 3 Thermophyical properties of stainless steel 304 and welding operational parameters[8] 表 3 304不锈钢平板的物性参数与焊接工艺参数[8] |
图4显示了弧柱中的电势(左)与电流密度(右)分布. 焊接时所加载的电压为24 V, 工件作为阳极, 由于接地而成为零等势体. 关注焊枪喷嘴中W阴极附近区域: 由图6a和b可知, Ar气等离子体温度很高, 则此处Ar气等离子体的电导率也很大, 参考图3c; 同时从图4中看出, 该区域电势梯度很大, 因而形成强电流密度, 进而产生大量的Joule热(即
图5显示了弧柱中电磁力的分布. 从电磁力的方向可以看出, 电磁力对电弧起收缩与加速的作用. W阴极尖端附近电磁力最大, 达到2.6×107 N/m3. 从矢量图中看出, 电磁力对电弧主要起收缩作用, 使弧柱直径变细, 提高其能量密度.
![]() | Fig.7 Distributions of velocity streamline and pressure in arc column at 2.0 s (p—pressure)图7 在2.0 s时刻弧柱中流线与压强分布 |
图6a是电弧及工件中速度(左)与温度(右)分布. 对于弧柱, W阴极尖端附近的温度最高, 达到35000 K, 如图6b所示. 喷嘴的压缩作用以及保护气的作用, 使弧柱等温线在工件上部的外围呈现出经典的“钟形”, 而在中心轴线处因进入小孔呈细长的“锥形”. 喷嘴出口处的弧柱中心轴线上轴向速度最大, 达到850 m/s, 与文献[35]中电弧速度相符. 高温与高速的结合使弧柱中温度分布更加均匀, 强化等离子弧射流的焊接效率与质量. 模拟结果表明, 沿弧柱中心轴线方向在离开W阴极尖端3~12 mm范围内, 电弧温度梯度很小, 也就是说从喷嘴出口到小孔内部Ar气等离子体的温度几乎保持一样高, 有利于热量沿金属厚度方向传输, 提高其熔透速率. 少部分Ar气等离子体从小孔底部流出, 温度和速度都很高, 速度几乎可达300 m/s; 大部分Ar气等离子体从工件上表面流出, 如图6c所示, 其温度和速度都相对较低. 高温等离子弧通过导热、对流与辐射方式将热量传递至工件. 当工件温度高于金属液相线温度(即熔化温度, 1723 K), 工件熔化形成熔池. 熔池在Marangoni力及切应力的作用下产生环流流动, 如图6d所示, 最大流动速度达到0.15 m/s. 熔池受对流传热的影响, 上部熔宽增大, 熔化轮廓线(熔合线)呈倒“喇叭形”. 工件中未熔化区域传热只有导热作用.
图7是弧柱中流线(左)与压强(右)分布. 高速Ar气等离子体冲击到小孔内壁面时速度急剧降低, 出现部分高压区和Ar气等离子体的返流现象. 喷嘴出口下方处极高速的Ar气等离子体会形成对保护气的卷吸作用, 从而保护气可以压制热等离子体而保护工件, 并防止高温熔化工件吸收空气中有害气体.
图8显示了电弧与工件中速度场(左)与温度场(右)随时间的演变过程, 不同时刻等温线的条数及其上对应的温度值都是相同的, 这样有利于清晰地比较分析温度场随时间的变化情况.
在电弧区, 初始阶段0.2 s时电弧自由凸起, 水冷喷嘴及保护气对其压缩作用尚未表现出来. 0.4 s时, 高温电弧在工件上表面被压低, “钟形”的电弧轮廓形成. 0.6~0.8 s时, 弧柱中外围电弧进一步被压低, 并出现尖端, 尖端与弧柱中轴线的距离为10 mm左右. 水冷喷嘴下方的低温区增大, 温度越低, Ar气等离子体热导率越小, 低热导率阻碍了热量的外散, 保证了弧柱中心附近的高温. 1.0 s以后, 弧柱温度场基本稳定. 弧柱中的速度场一直在变化. 高速Ar气等离子体喷射到小孔内部斜壁面上时, 速度迅速减小, 出现Ar气等离子体返流. 由于速度急剧降低, 在小孔内部会出现部分高压区, 阻碍Ar气等离子体的向下冲击, 700 m/s以上速度区域沿轴向逐渐向喷嘴回缩. 高速等离子弧的直径收缩得非常细, 1.0 s以后, 300 m/s以上的高速等离子弧都集中在直径不到2 mm的柱状区域内, 使弧柱的能量密度更加集中.
在工件区, 0.6 s时工件开始熔化, 出现熔合线(即为1723 K的液相线). 1.0 s时, 熔池变大, 由于熔池流动较弱, 流动对熔池内传热影响较小. 1.4 s时刻, 熔池中出现明显的环流流动, 这是由于Marangoni力的作用引起的. 随后熔池逐渐变大, 同时热影响区也加深; 熔池内流动速度也逐渐增大, 最大流速达到0.15 m/s. 1.8 s之后, 整个工件被完全熔透, 熔合线到达小孔的下表面, 熔池内流动加强并促进了熔池中的传热, 出现明显的倒“喇叭形”熔合线.
为了对焊枪设计以及PAW焊接工艺提供优化指导, 本工作对其中的结构参数与工艺操作参数进行模拟正交试验分析. 结构参数包括焊枪的电极间距、电极内缩量、喷嘴孔径以及小孔的上表面半径, 操作参数有焊接电流、工作气体流量、保护气流量. 总共7个因素, 每个因素3水平, 如表4所示. 对于3水平7因素的正交模拟分析, 需要设计18组试验, 记为L187). 由于在实际的焊接实验中, 小孔上表面宽度的观测比较困难, 这使得其实际大小无法被准确确定, 因此通过模拟来预测小孔上表面尺寸的可能大小.
![]() | Table 4 Table of factors and levels for orthogonal test simulation 表4 正交试验模拟因素水平表 |
为了研究PAW焊接各因素的主次关系, 对试验中的7个因素进行极差分析, 如图10所示. 以焊缝的上部与底部熔宽作为考核指标, 因为它们最能反映焊缝的几何形状及焊接质量. 从图中可以看出, 在PAW焊接过程中, 电极间距、电极内缩量、喷嘴孔径对应的上、底部熔宽极差数是较大的; 即焊枪的结构参数对焊缝熔宽影响很大, 它们应该是PAW焊接工艺的重点优化内容. 尤其是, 对应图中最大极差数的电极内缩量, 在PAW焊接过程中必须慎重确定, 因为电极内缩量对弧柱中电流密度分布及对弧柱压缩影响甚大, 进而影响高温电弧向工件的冲击与传热, 最终显著影响焊缝的熔宽. 相比于结构参数, 焊接电流、工作气体流量、保护气流量等工艺操作参数对应的上、底部熔宽的极差数较小, 即焊缝熔宽受这些工艺操作参数的影响小于焊枪的结构参数.
(1) 等离子弧的外围在工件上部呈现出经典“钟形”, 而在中心轴线处因进入小孔呈细长的“锥形”; W阴极尖端附近Ar气等离子体能量密度高度集中, 该处温度最高可达35000 K; 等离子弧的高速区集中在弧柱的中心轴线上; 当高速Ar气等离子体冲击到小孔壁面时, 其速度急剧降低, 小孔内出现高压区和Ar气等离子体的返流现象.
(2) 熔池在Marangoni力及切应力等作用下产生环流流动, 焊缝熔合线呈倒“喇叭形”状.
(3) 相对于工艺操作参数, 焊枪的结构参数对焊缝熔宽(反映焊缝几何形状及焊接质量)的影响更显著, 需要予以重点考虑电极间距、电极内缩量和喷嘴孔径.
[1] |
|
[2] |
|
[3] |
|
[4] |
|
[5] |
|
[6] |
|
[7] |
|
[8] |
|
[9] |
|
[10] |
|
[11] |
|
[12] |
|
[13] |
|
[14] |
|
[15] |
|
[16] |
|
[17] |
|
[18] |
|
[19] |
|
[20] |
|
[21] |
|
[22] |
|
[23] |
|
[24] |
|
[25] |
|
[26] |
|
[27] |
|
[28] |
|
[29] |
|
[30] |
|
[31] |
|
[32] |
|
[33] |
|
[34] |
|
[35] |
|